Blog
CATEGORIES
Cement plant facility managers understand the importance of limiting downtime and ensuring cement silos maintain optimum storage capacities. However, without a routine inspection, cleaning, and maintenance schedule, moisture intrusion and/or impaction can lead to material buildup, blockages, and material flow issues. Air pads and other fluidizing equipment also needs to be inspected and serviced regularly by a professional silo cleaning company to ensure correct operation. These common silo problems can cause shifts in the production schedule that greatly impact the bottom line.
How do you clean a cement silo?
USA Silo Service can clean, inspect, and maintain your cement storage silo or dome. For nearly thirty years, we've repeatedly seen that our enhanced pneumatic cleaning method with our proprietary cleanout head, The Boss™, is the most powerful silo cleaning method available. The USA Silo Service cleaning solution is 2/3 more powerful than conventional cleaning methods. In addition, since The Boss moves more material per hour, our system delivers optimal cleaning quickly and correctly, resulting in less downtime and production loss, ultimately saving you money.
How do you improve cement plant operations?
Cleaning, inspecting, and maintaining your cement silo is one of the best ways to improve your cement plant operations. A clean, well-maintained silo not only helps you stick to production schedules and yield maximum production, it also helps you ensure the quality of your product and protect employee safety.
Schedule your next silo cleaning today. The Boss silo cleaning machine and USA Silo Service can help you return to a regular silo cleaning schedule to maximize efficiency, production, and safety.
|
Fast-Track Your Next Silo Cleaning
Hung-up, clogged or slow-running silos are a problem. They impact efficiency and hurt your bottom line - not to mention your silo structure. The Boss™ accelerates the cleaning process, minimizing downtime and time spent on-site to give you immediate cost savings. Our proprietary system moves more material than conventional silo cleaning methods so our customers can return their silos to full capacity more quickly. With over 30 years of silo cleaning experience, USA Silo Services has seen numerous cases where material buildup hampered productivity. Check out a few of these examples below.
|
Fast-Track Your Next Silo Cleaning
Hung-up, clogged or slow-running silos are a problem. They impact efficiency and hurt your bottom line - not to mention your silo structure. The Boss™ accelerates the cleaning process, minimizing downtime and time spent on-site to give you immediate cost savings. Our proprietary system moves more material than conventional silo cleaning methods so our customers can return their silos to full capacity more quickly. With over 30 years of silo cleaning experience, USA Silo Services has seen numerous cases where material buildup hampered productivity. Check out a few of these examples below.
|
![]() |
Gypsum Byproduct Silo Cleaning
|
|
A gypsum silo with significant product buildup along the walls created a productivity bottleneck. The silo suffered from rat holing that allowed for only restrictive material flow and reduced the storage capacity by 75%. Using The Boss silo cleaning machine, USA Silo Service restored the production schedule in only a few days.
|
Gypsum Byproduct Silo Cleaning
|
A gypsum silo with significant product buildup along the walls created a productivity bottleneck. The silo suffered from rat holing that allowed for only restrictive material flow and reduced the storage capacity by 75%. Using The Boss silo cleaning machine, USA Silo Service restored the production schedule in only a few days.
|
![]() |
Fly Ash Silo Cleaning
|
|
A fly ash storage silo experienced restricted, asymmetric material flow that slowed production times. Unlike the above gypsum byproduct silo cleaning example, this case was due to several rat holes above the discharge points. To clean this silo, USA Silo Service first had to remove material buildup down through the silo cone.
|
Fly Ash Silo Cleaning
|
A fly ash storage silo experienced restricted, asymmetric material flow that slowed production times. Unlike the above gypsum byproduct silo cleaning example, this case was due to several rat holes above the discharge points. To clean this silo, USA Silo Service first had to remove material buildup down through the silo cone.
|
![]() |
Coal Silo Cleaning
|
|
A coal storage silo experiencing production delays and asymmetric flow was found to have buildup above the cone level and plugged discharge chutes at the cone bottom. In addition to causing slow material discharge, the issues caused asymmetric flow damaging the silo wall. USA Silo Service quickly removed the blockages before additional structural damage was caused.
|
Coal Silo Cleaning
|
A coal storage silo experiencing production delays and asymmetric flow was found to have buildup above the cone level and plugged discharge chutes at the cone bottom. In addition to causing slow material discharge, the issues caused asymmetric flow damaging the silo wall. USA Silo Service quickly removed the blockages before additional structural damage was caused.
|
REQUEST A SILO CLEANING QUOTE
No matter the silo type or stored material, USA Silo Service can meet your silo cleaning needs.
|
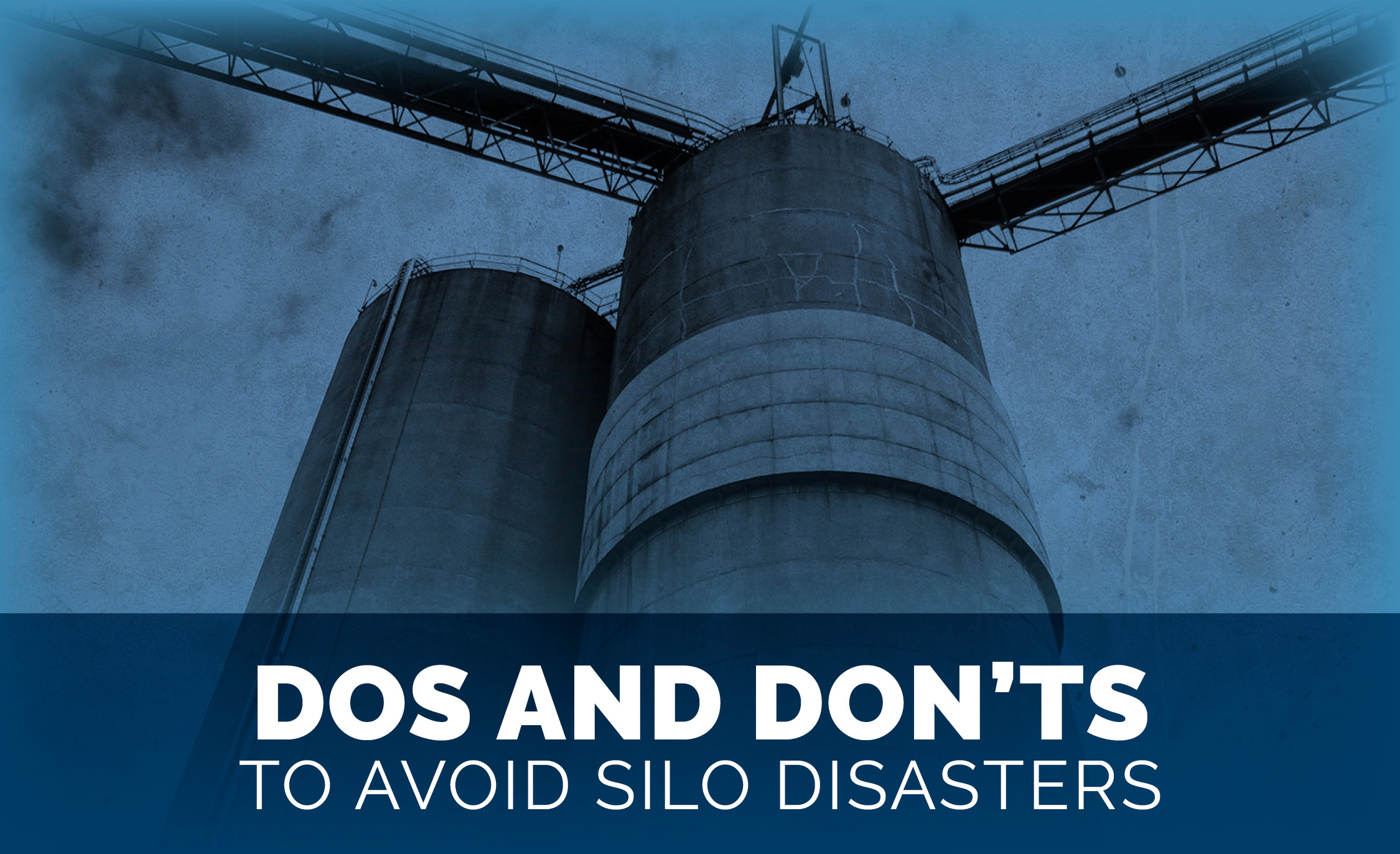
Modern silos have been used since the late 19th century. Yet since that time, their design, construction, and recommended maintenance services have undergone drastic changes to improve safety. Here are the top ways facility owners and managers can help prevent storage silo disasters.
|
|
Is your silo in need of repair or restoration? Contact us today for a quote.