Blog
CATEGORIES
Silos are unique structures, and waterproofing coatings are not created equal. Silo coatings like floating membranes and roofing tar are some of the cheapest to acquire. However, they are also the most likely to fail during the normal use of a metal or concrete silo. Membranes are easily punctured during routine loading and unloading or even through heavy foot traffic. Roofing tar, on the other hand, cannot tolerate foot traffic. Tar also naturally softens by the sun, allowing stored material to stick into the surface and create buildup that is extremely difficult to remove. In cold weather, tar solidifies and can easily crack and allow moisture to penetrate the silo and jeopardize stored material. Sprayed polyurethane coatings similarly do not tolerate foot traffic, are easily punctured and are sensitive to humidity.
The most effective, monolithic barrier against moisture is a rubberized coating that bonds directly to various surfaces to repair cracks and seal penetrations, laps and fasteners. Rubberized coatings have a high elasticity coefficient that moves with silo vibration caused by roof-mounted equipment or loading and unloading.
Our rubber coating reduces costly reapplications of surface protectants and can be applied to many surfaces. As a silo roof coating, our rubber coating can fix both metal silo roofs and concrete silo roofs. In addition, our silo roof-top coating has the flexibility to maintain its integrity through the changing seasons, protect against oxidation, humidity and corrosive environments while resisting alkali, salts, abrasions and fumes.
Rubber Roof-Top Coating Works On:
- Metal buildings and roofs
- Built-up roof (BUR) membranes
- Grain silos and bins
- Silo exterior walls
- Single-ply roofs
- Urethane foam roofs
- Steel bolted joints
- Concrete silo roofs
Additional Benefits of Rubberized Silo Coatings:
- Not a floating membrane
- Offers excellent adhesion to aluminum, galvanized steel, painted surfaces, modified bitumen, steel joints and many other surfaces
- Excellent in sealing cracks, laps, fasteners and roof surface penetrations
- Available in all 50 states and a variety of colors
Our roof-top silo coating method is a proven industrial roof coating system that keeps elements out and stored materials dry. Request a quote from us today.
Proper material flow in silos is important for more than just production schedules. Issues with material flow can cause increased stress on silo walls that may go beyond what the silo was designed to withstand. Not only does this cause cracking, spalling and possible wall separation, it can also lead to structural failure.
Silos that were initially designed with internal reinforcement sometimes face cracking or delamination of the concrete. When this is seen on the silo exterior, it is important to schedule a silo inspection as soon as possible. Such damages are often caused by overstressing of the horizontal reinforcing as a result of material flow issues.
What is silo post-tensioning?
Tension is a critical component in silo repair. If the silo is still structurally sound, certain damages caused by failing interior steel reinforcement can be repaired by post-tensioning. Post-tensioning silo repair uses high-strength post-tensioning strands that are placed around the exterior of the silo. These tensioned bands essential take over the structural support of the original internal steel by keeping walls sturdy against additional stress caused by asymmetric flow.
During this restoration process, a qualified engineer uses factors such as silo size, stored material weight and how the silo is used to determine tension specifications necessary specifications for wall reinforcement. After the strands are properly tensioned through a hydraulic process, steel lock couplers are positioned and tightened. Once completed, the tensioning assures that the silo can be safely used. Once the silo is restored through post-tensioning, it can then be returned to its actual load capacity.
Request a silo repair quote by scheduling your inspection today.
View our video, How Often Should I Have My Silo Inspected, or view our full library of videos on silo inspection, silo maintenance, and silo restoration on 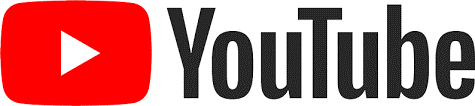
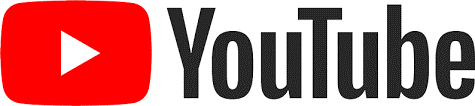
Silo cleaning is an essential part of silo ownership. It also saves you money and maximizes production and profit. Avoiding compaction and hydration of material through regular emptying and cleaning keeps your silo in proper working order. When stored material becomes too compacted, it must be removed by a professional cleaning company. An efficiently working silo helps you meet production goals.
By removing material buildup, silos are returned to their original storage capacity, and material flow issues that can slow down production are corrected. Clogged or slow running silos are a problem that will interfere with efficiency and profitability. Material buildup deters the silo from reaching its full capacity. Once a silo begins to lose flow, this accelerates the buildup over time and can lead to additional blockages. Removing this buildup can also allow you to recover lost material. Our professional team maximizes the cost-effectiveness of your silo cleaning operations by supplying the necessary industrial vacuum truck services to meet the requirements of your situation.
The Boss - Silo Cleaning Techniques
Professional silo cleaning companies typically use a remote, dry cleaning system to remove stubborn material buildup. The most powerful system available in the U.S. is a unique clean-out head, The Boss, proprietary to USA Silo Service that is 65% more powerful than other pneumatic systems. By removing more material faster and more efficiently than any other clean-out method, including the whip system, The Boss accelerates the cleaning process. This minimizes downtime and time spent on-site, providing immediate cost savings.
The Boss is a unique clean-out head designed to accommodate variable attachments selected by our field crews to match the type of material being removed. Our silo cleaning technique includes operating in a systematic pattern within the silo to remove the toughest buildups.
The Takeaway
Regularly cleaning your silo can help keep it operating efficiently and limit potential liabilities. Regular cleanings also increase your silo's usable lifespan, minimize big-ticket repairs, and avoid more costly cleaning expenses. In addition, professional silo cleaning saves you time and money by removing buildup and recovering lost material.
USA Silo Service, Inc. is a silo and bin cleaning, bulk storage removal/clean-out and industrial coating corporation that has serviced the needs of the industry for almost thirty years. Our silo cleaning services have been successfully performed throughout the United States and Canada and have proven benefits for our customers. USA Silo Service also provides vacuum truck and material disposal services to assist in removing and relocating silo debris. Our professional team also responds quickly to emergency silo cleaning needs.
Check out our full library of videos on silo cleaning, construction, inspection and repair on
for more information.
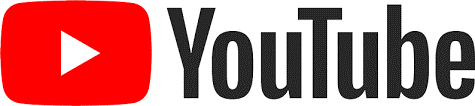